Freshly painted and well-equipped
With DACHSER’s help, WAGNER Spraytech UK is getting ready for further growth. And for Brexit. A new warehouse makes it easier to overcome the challenges.
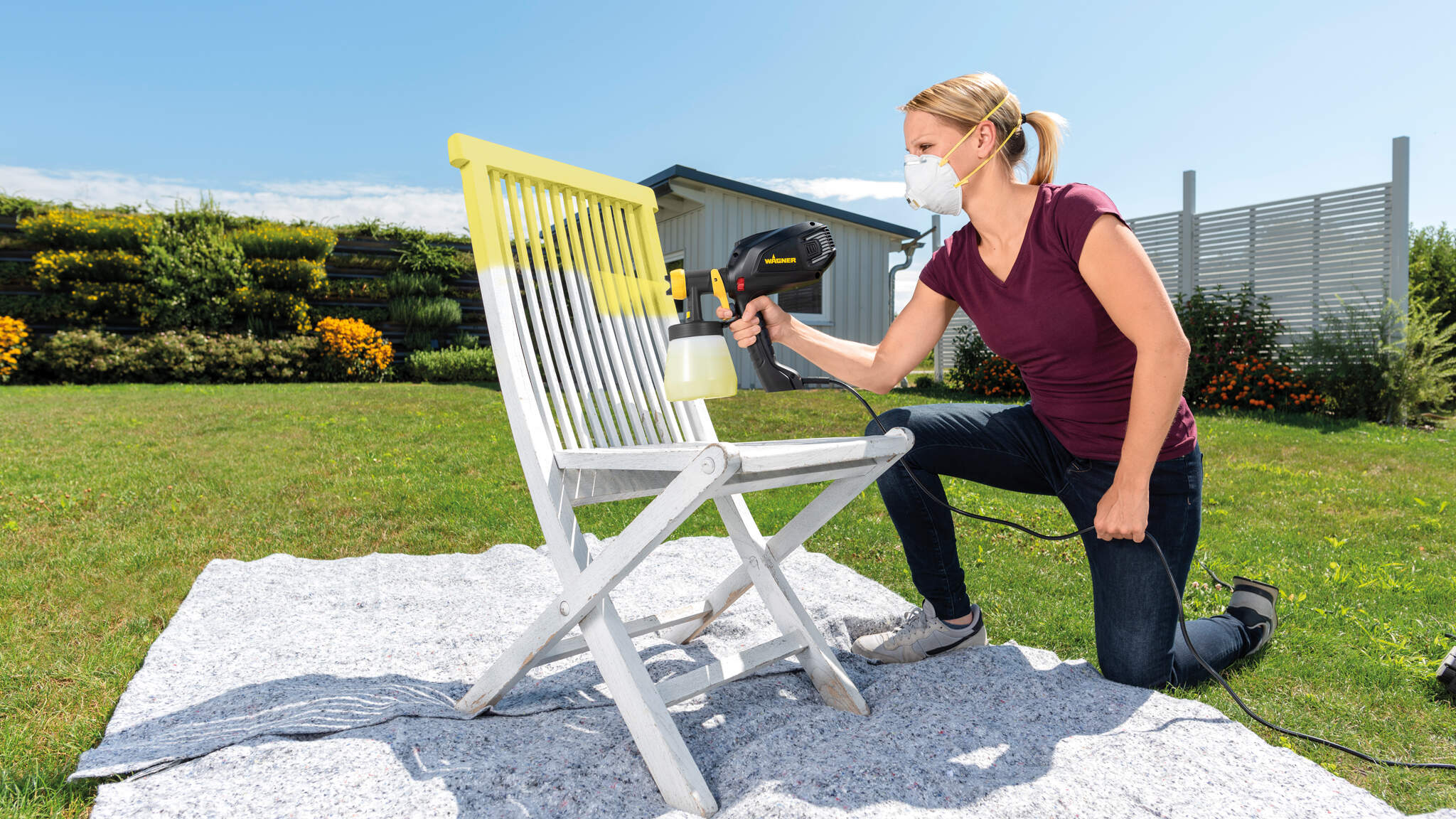
Companies are currently finding it difficult to prepare for the future, what with all the unanswered questions and uncertainties surrounding Brexit. “With Brexit on the horizon, there’s never a dull moment,” comments Maciej Kwiek, Business Development Manager for contract logistics at DACHSER UK. The native Pole seems to have mastered the typical British mix of composure and humor. “We’re responding to the developments and keeping in close contact with our customers,” he continues.
After all, business has to go on, Brexit or no Brexit. “We’re concentrating on the projects we have in the pipeline,” Kwiek says. One of DACHSER’s focuses at the moment is the UK DIY market. Chains such as Wilko, Kingfisher, Homebase or Wickes are as popular there as Obi, Hornbach, and the rest are here in Germany. Products from Switzerland’s WAGNER Group can be found in almost every DIY store. Its product portfolio ranges from paint spray systems for DIY home improvements to professional coating, painting, and cleaning sprayers and industrial coating systems.
Last year, WAGNER’s UK business ran into a problem, and for once it had nothing to do with Brexit: at its warehouse in Guildford, just southwest of London, WAGNER Spraytech UK reached its capacity limits. In a short space of time, DACHSER took over warehousing operations and moved them to an existing logistics center in Northampton, some 100 kilometers north of London.
Value-added services and flexibility
“The move was a challenge,” Kwiek admits. Everything had to happen on a tight schedule. Ian Pocock, Customer Service Manager at WAGNER Spraytech UK, recalls: “We had to clear out the warehouse in Guildford and relocate the whole inventory to Northampton while ensuring there was no disruption to our customer deliveries”. But in this case, both parties had made thorough plans in advance. Kwiek continues: “This is a good example of how important it is to be prepared, communicate transparently with the customer, and establish a proper schedule.”
In Northampton, the goods are prepared according to the customer’s strict requirements. DACHSER also carries out comprehensive value-added services, such as unloading incoming goods from containers onto unmixed pallets, inspecting the high-quality goods, providing spare parts logistics, managing returns, and shipping the products to online retailers. In this way, DACHSER coordinates more than 270 different items for WAGNER, utilizing 3,500 pallet spaces.
As things stand, though, it’s impossibe for Northampton to avoid Brexit completely. “In preparation, we’ve increased inventory levels of our most important fast-moving products to give us a three- to four-month buffer,” Pocock explains. In addition, DACHSER’s MIKADO warehouse management software enables a considerable degree of flexibility. Kwiek, too, is optimistic about the future. “Our experience means we can overcome any challenge the market throws at us, with flexibility and adaptability.” Even Brexit.