The digital twin: Dachser and Fraunhofer IML increase transparency in groupage handling
Successful test operations at two locations. The first step eliminates the need to manually scan and label packages and speeds up departure times. Going forward, it is hoped that AI will also support and optimize loading.
In collaboration with Fraunhofer IML, Dachser has developed an innovation in groupage logistics and implemented it in a practical setting. In what is known as the @ILO terminal, a complete digital image of all a transit terminal’s packages, assets, and processes—a “digital twin”—is created fully automatically and in real time. The digital twin speeds up inbound and outbound processes and provides continuously updated information on the location of each package, benefitting not only logistics operatives and drivers, but also employees in scheduling and customer service.
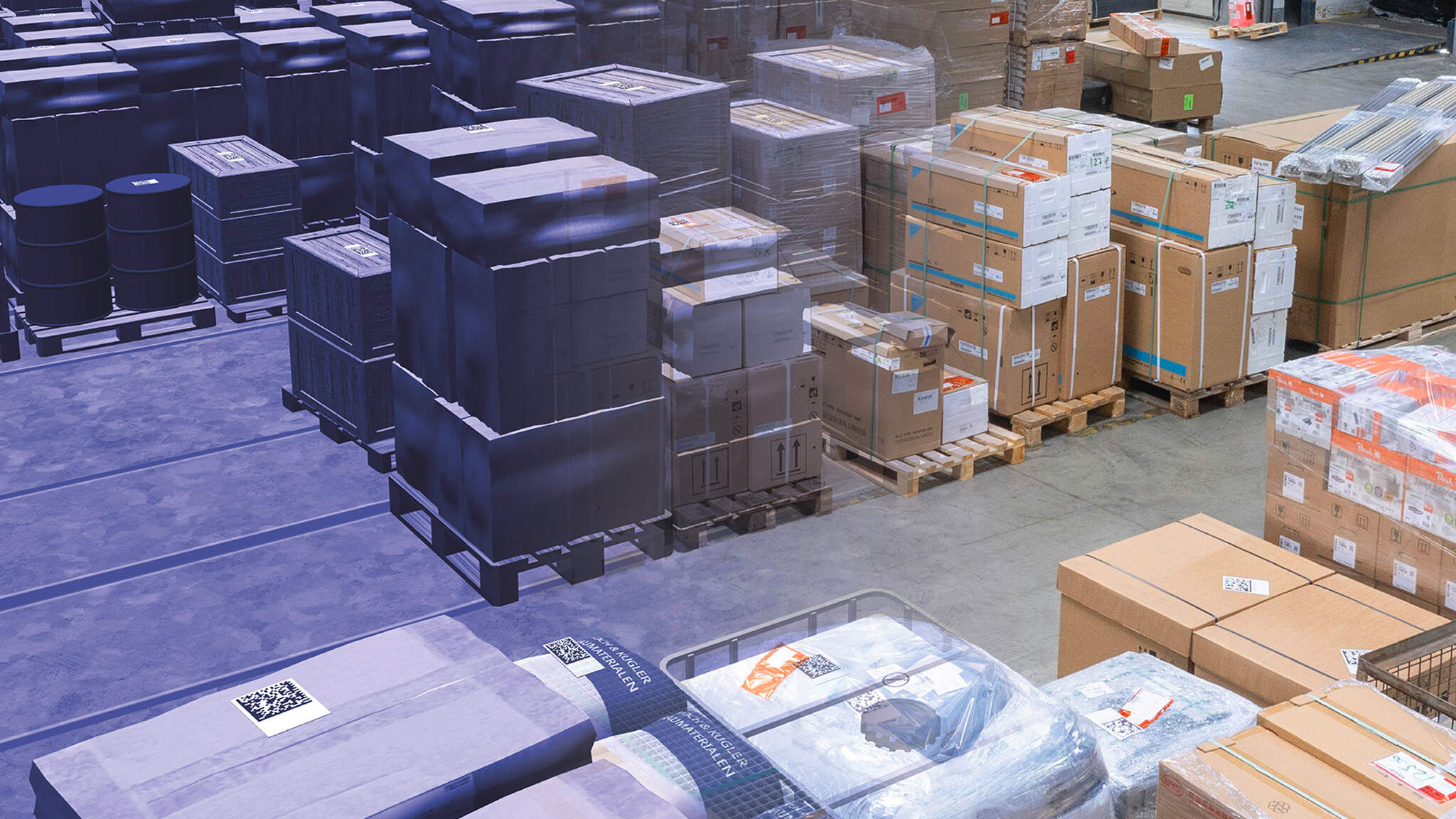
This technological innovation is already proving its worth under real operating conditions in the transit terminals of the Dachser branches in Unterschleißheim near Munich and Öhringen near Heilbronn. @ILO stands for Advanced Indoor Localization and Operations and is a research project from the DACHSER Enterprise Lab, which the logistics provider operates together with the Fraunhofer Institute for Material Flow and Logistics IML. The core of the project is the jointly developed @ILO software. Special AI-based algorithms interpret the data that the optical scanning units capture every second, using it to automatically and immediately identify and locate all packages. In the future, they will also measure the packages. This creates a complete, always up-to-date image of the terminal and its processes—a digital twin. In the future, it is expected to provide real-time data on every palletized shipment in Dachser’s European transport network.
“Consistently digitalizing our core processes will enable us to further improve our service,” explains Dachser CEO Burkhard Eling. “We are not focusing solely on state-of-the-art technologies to make that happen—we also want to bring our employees into the digital world, just like in the @ILO terminal. This innovation offers clear advantages for day-to-day work in the transit terminal and thus has the potential to be a milestone on the road to more efficient and sustainable logistics operations.”
“The @ILO terminal takes us to a new level of supply chain visibility,” says Stefan Hohm, CDO and member of the Executive Board at Dachser. “We worked on the digital twin with Fraunhofer IML for over four years. With a lot of knowledge, ideas, and above all passion, the teams—which are made up of both researchers and experts who work in the field—have made the internet of things and the vision of Logistics 4.0 a reality in groupage logistics, too.”

Consistently digitalizing our core processes will enable us to further improve our service.
Burkhard Eling, DACHSER CEOFully automatic identification and accurate tracking down to the meter
In the @ILO terminal, packages are identified fully automatically when they enter and leave, as well as during their stay, and are recorded in the transport management system. This eliminates manual barcode scanning and the additional labeling of the packages. Two-dimensional data matrix codes on the top of each package serve as identifiers and, together with several hundred optical scanning units in the facilities’ ceiling area that capture the entire floor, provide the technological basis of this system.
This setup also enables accurate tracking, down to the meter and in real time, of all pallets throughout the transit terminals, which can often be the size of a soccer field. The locations of shipments and the position of ground conveyors can be visualized in real-time and displayed on websites, apps, or mobile displays together with instructions for internal transport, significantly improving transparency in the warehouse and speeding up searching and loading processes.
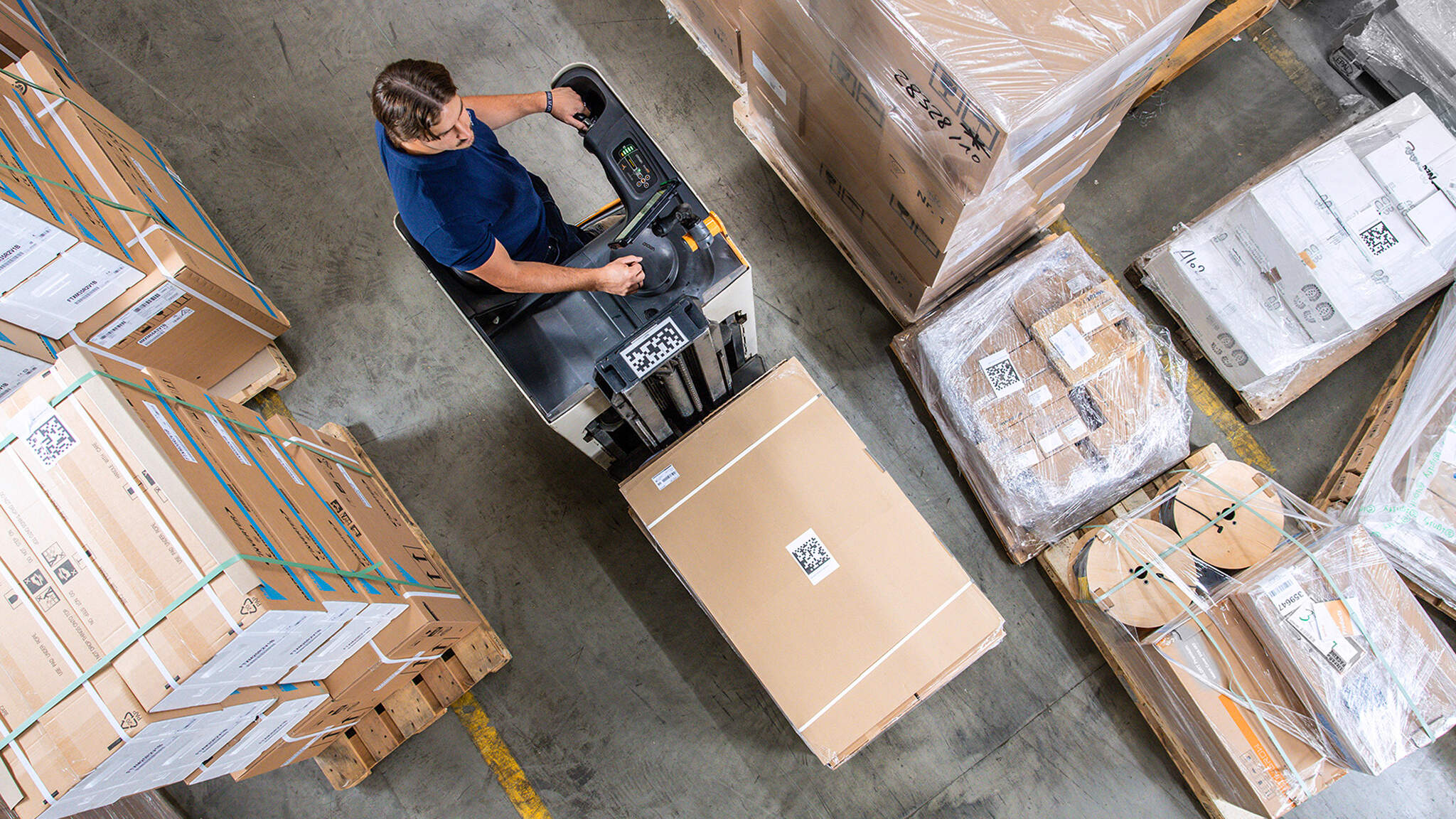
The automatic “wedding” of the ground conveyors and packages is a novelty. The @ILO system automatically detects when a ground conveyor picks up a pallet, and transmits information on each package to employee displays in real time. This is another function that cuts process times and can reshape processes in the transit terminal.
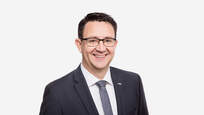
The @ILO terminal takes us to a new level of supply chain visibility.
Stefan Hohm, DACHSER CDOConstant measurement of packages
A further technological highlight of the @ILO terminal is in the pipeline: the fully automatic and constant measurement of all packages. The system is already able to identify package dimensions with great accuracy in pilot operations. When the system is fully ready for hands-on use, the volume data obtained on each package could be fed into intelligent algorithms to, for instance, assist drivers and transit terminal employees with loading and route planning, and to further increase the capacity utilization of swap bodies, trailers, and local transport vehicles. The result would be a reduction in transport kilometers and thus also a reduction in emissions.
“Initial tests have already clearly demonstrated the practical advantages of the @ILO terminal,” says Alexander Tonn, COO Road Logistics at Dachser. “The system saves our employees valuable time and lets them organize processes in the terminal even more efficiently. It also makes loading and departure significantly less stressful for drivers. All this has the potential to bring next-level innovation to groupage logistics.”
Detailed information on the @ILO project is available in the following PDF.