Robotic maneuvers
Logistics holds so much potential for autonomous vehicles. One use for them is as a way to fully automate the process of maneuvering swap bodies. But how can this be done safely and efficiently in a busy freight yard? DACHSER’s Langenau site near Ulm researched this under real operating conditions.
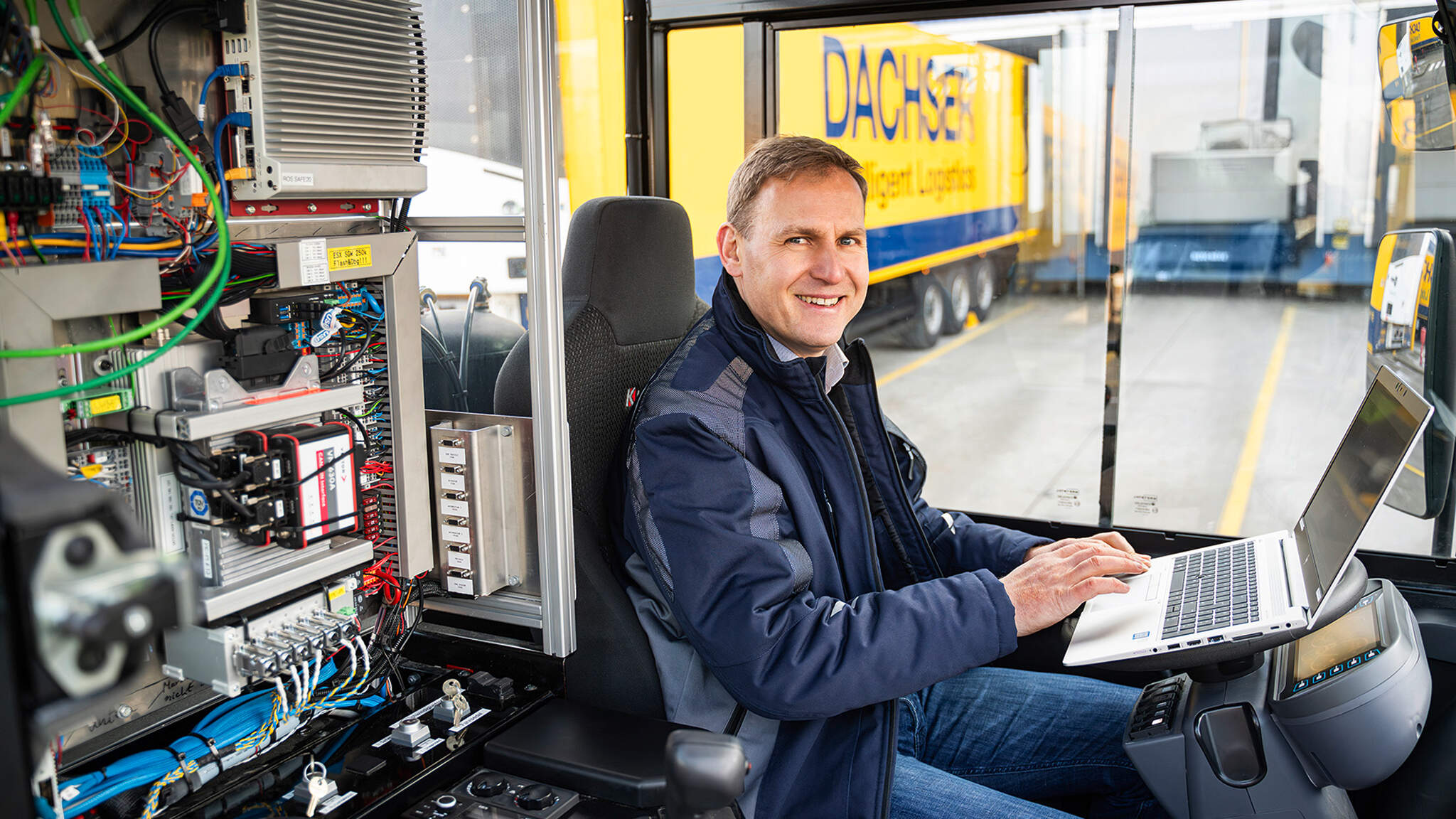
The Kamag PrecisionTractor picks up an empty semi-trailer from the parking lot and makes its way to Gate 35. The person at the wheel can lean back and relax, because the articulated truck is driving autonomously. And something else stands out: the tractor unit’s front bumper is sporting three large round sensors, one at each end and one in the middle, from which bright green cables branch off into the vehicle’s digital innards; there are more sensors and antennas on the roof.
At the depot of the DACHSER branch in Langenau, in southwestern Germany, a vision of the future is becoming reality: the SAFE20 research project, funded by the German Federal Ministry for Economic Affairs and Climate Action, is testing the regular operation of fully automated vehicles at depots. And the two autonomous yard vehicles in use here are hard at work. At speeds of up to 20 kilometers per hour, they fit seamlessly into the mix of human-driven vehicles and pedestrians. Accompanied only by a safety driver, who is ready to intervene in an emergency, the vehicles built by yard logistics specialist Kamag have to deal with many uncertainties en route, avoiding obstacles, changing direction, and watching out for pedestrians and cross traffic. This is a real challenge for their sensor technology and the associated IT. Lidar scanners use laser light to capture and create a digital image of their surroundings. A GPS antenna on the roof ensures precise positioning of the vehicle while on the move. The second antenna receives data from external infrastructure sensors, providing the vehicle with information obtained from radar and camera data. “There’s huge potential to automate the maneuvering of swap bodies and trailers from where they’re parked to the transit terminal for loading and unloading—especially given the shortage of drivers,” says Stefan Hohm, Chief Development Officer at DACHSER.
To enable completely safe automated truck transports in a logistics facility—a complex process—the research project also installed cameras and sensors on the exterior of the buildings. If one of these detects, say, someone crossing a crosswalk, the autonomous vehicle gets an advance warning. That way, it can reduce its speed and, if necessary, immediately come to a stop even before it turns the corner and the person comes into view.
Integrated into the traffic flow
“For mixed operation in our yard, it’s crucial that the autonomous vehicles not become an obstacle,” says André Bilz, Team Leader Truck & Terminal Equipment at DACHSER’s Head Office. As things stand, the applicable safety regulations specify that such vehicles may operate only at speeds of 6 to 8 kph. The vehicles being tested here, however, are three times as fast, traveling at up to 20 kph. They have to fit into the “normal” flow of traffic alongside drivers in their trucks as well as other vehicles and pedestrians at the depot. “In yard service, we’ve assigned demanding transport tasks within the automation zone—such as moving swap bodies and semi-trailers around—to special vehicles that carry them out completely autonomously,” Bilz eplains.
The research project has now spent three and a half years investigating how this works in practice in a logistics operations context. Important foundations were laid, such as a comprehensive safety concept that was validated in continuous operation under real conditions. The project results are now set to be incorporated into the development of a legally compliant framework for automated freight transport at transit terminals. In addition to DACHSER, another seven partners are involved in SAFE20. These include the Fraunhofer Institutes for Material Flow and Logistics IML and for Transportation and Infrastructure Systems IVI. ZF Commercial Vehicle Systems from Hannover acted as project coordinator and was responsible for converting the Kamag PT truck tractor. Kamag Transporttechnik supplied the two special vehicles, which the various partners then equipped with appropriate sensors and on-board electronics for data processing. SICK AG, which specializes in this field, supplied the sensors and was in charge of drawing up the safety concept. As an automation expert, Götting supplied essential components for vehicle positioning.
As things stand, the applicable safety regulations specify that such vehicles may operate only at speeds of 6 to 8 kph.
André Bilz and Christoph Ehrhardt, Department Head Trends and Technology Research in the Corporate Research & Development division, are pleased with how the large-scale test has run under real conditions: “We don’t have a production-ready solution yet, but we have been able to collect valuable experience and data that we can use to shape the way forward,” Ehrhardt says. Bilz adds that it would now be possible to demonstrate that safe mixed operation is feasible. “In addition to increased process reliability, we also expect a noticeable reduction in collision damage,” he says. The vehicles can maneuver not only swap bodies but also semi-trailers.
In both cases, driving must be accurate down to the centimeter. The sensors are always fully alert and never distracted, and they also work when lighting conditions are difficult, such as at dusk or dawn. “We did occasionally have trouble in extremely bad weather conditions such as heavy snowfall, but these issues are solvable.”
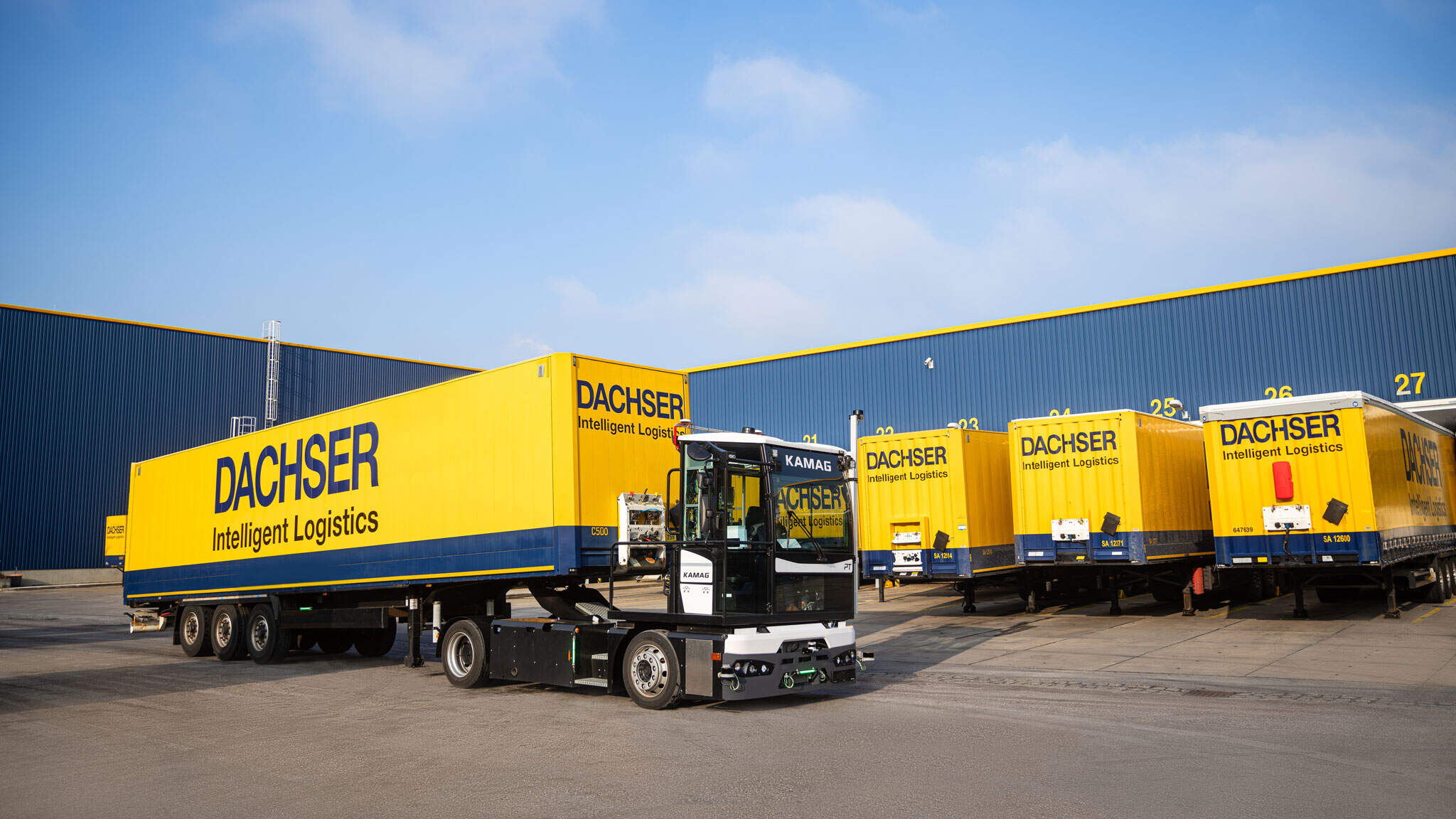
Valuable addition
In times of acute driver shortages, autonomous vehicles can provide useful support. However, they can’t yet perform yard maneuvers entirely without people. Tasks such as securing the trailer with wheel chocks or opening and closing the doors still have to be done manually. Processes have been defined for this. In some cases, the loading staff must also take responsibility. An automatic coupling system was installed both to handle automatic coupling and to connect compressed air for the braking system as well as electricity for the lighting. However, having to equip every trailer with such a system would have a negative impact on profitability. Moving swap bodies is much easier.
A key outcome of SAFE20 is how it has identified improvement potential for future market solutions. But there’s one thing this groundbreaking research project shows for certain: the goal of integrating autonomous vehicles safely and economically into logistics operations on a closed site is within reach.
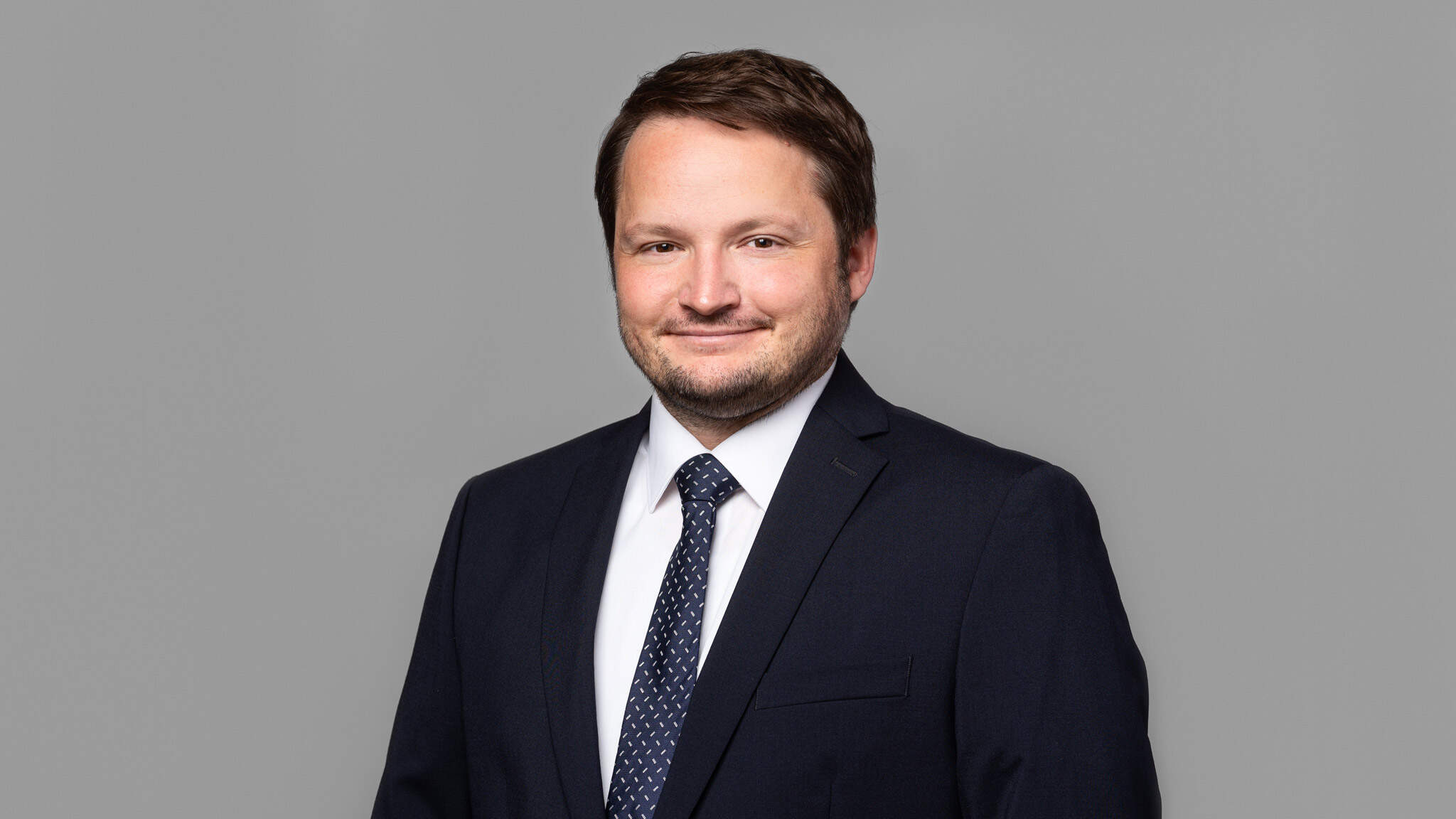